Reduce the Burden on Quality With NIR
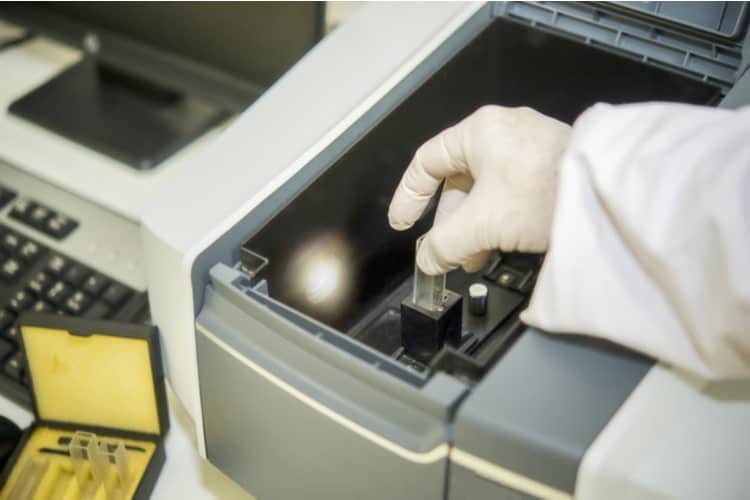
Product quality ensures that manufacturers can remain competitive while exceeding customer satisfaction through products that demonstrate reliability, lowered cost and increased performance.
However, as quality standards are continuously pushed higher by regulators, so too are costs driven higher, coupled with an increased burden on quality. New technologies are the key to combating the rising costs and elevated pressures faced by the quality department.
Traditional quality frameworks have relied on small windows into the manufacturing process, which are derived from routine sampling. From these samples, assessments are made to ensure the process is within specification with respect to defined critical process parameters (CPP) and critical quality attributes (CQA) for the process.
Routine sampling offers limited insights that may not be reflective of the process as a whole. Using advanced process analytical technologies (PAT), such as Multieye2 near-infrared spectrometer, manufacturers can shift to a real-time, continuous monitoring framework.
Reduce testing time, increase quality
With Multieye2, immediate quality control feedback is available to the quality department, giving near-boundless levels of insight. With substantially greater data points, quality assessments can be made with vastly increased rates of confidence.
Typically, the analytical laboratory would carry out time-consuming sample activities, such as Karl Fisher for moisture content, and HPLC for blend uniformity or density measurements.
Due to the long-lead times of these tests, careful coordination is required to maintain adequate sampling and analysis. However, such systems are not agile and can be disrupted by changes in manufacturing priority.
Using Multieye2, moisture, blend uniformity, and blend density measurements can be read continuously in real-time, which grants the ability to adjust CPPs on the fly to avoid losing batches due to going out of specification. The result of digitising a process with Multieye2 leads to more robust quality assurance and control activities.
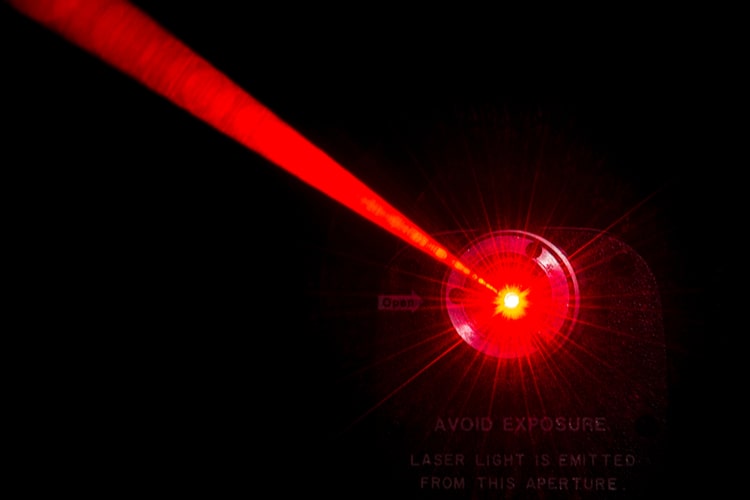
Getting smart with NIR
The large datasets that Multieye2 generates in real-time are extremely valuable in conjunction with an automated control platform, like SmartX. Coupling a continuous feed of process data and insights into SmartX from Multieye2 allows for Predictive Quality Analytics (PQA). PQA is widely used to estimate the quality of products, materials and components within the production process.
SmartX analyses the vast scale of data obtained during the production process and applies advanced data analytics and machine learning to derive critical insights.
These insights let manufactures detect patterns, critical variabilities, or even predict future outcomes. Taking this approach leads to a proactive quality strategy, whereby abnormalities in the process can be predicted, and the root cause addressed before the occurrence of a quality issue.
Using the advanced technologies found in Multieye2 and SmartX let us shift away from traditional methods of quality assurance and quality control. The move to the smart factory eases the burden on quality, while increasing quality standard through fewer reworks, reduced losses and immediate quality control feedback.
To learn more about how Multieye2 and SmartX can propel you to higher standards of quality, get in touch with us!
At InnoGlobal Technology (formerly Innopharma Technology), we are driven to push the boundaries of industry and share our knowledge. Follow us on LinkedIn and Twitter for more exciting developments from trailblazing R&D to Industry 4.0!