Before we had any PAT tools, the process was like a black box to us. We put something in and get something out without knowing what happened inside. Now, we have an ‘Eye’ to look inside that black box and see what’s going on in there.
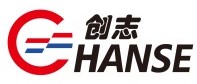
SmartX is an Industry 4.0 process automation solution which supports pharmaceutical process development from studies and DoE to scale-up and manufacturing. This platform provides secure storage, advanced analytics, process insights and flexible automation tools ensuring efficiency, productivity, process robustness and patient safety in every dose.
SmartX provides process operation-specific control and connectivity, without the need for extensive customisation. The highly adaptable Data Broker module allows connection to a vast range of sensor technologies, MES and data historians. Existing or new process equipment can be easily integrated, all provided and configured by InnoGlobal Technology (formerly Innopharma Technology), without the need for third-party systems integrators.
Remotely accessible process dashboard enables rapid batch analysis, process trending, failure prediction and investigation across the organisation. Advanced Dynamic Process Control (ADPC) provides user-friendly automation, with a wide range of chainable pre-configured functions for specific process types. First-principles models are leveraged for scale and equipment independence, optimising transferability and scale-up. Simple PAT integration enables CQA-driven processing with maximum robustness to raw material changes.
Simple and secure handling of data ensures Data Integrity by Design from experimentation and DoE to process data storage. Data storage can be implemented in either a cloud or edge (on-site) model. Data security and audit trail functionality provide a fully 21 CFR part 11 compliant system with comprehensive user access control covering process data, process definitions, analytics techniques, and automation configurations.