The Changing Face Of Cosmetics Manufacturing
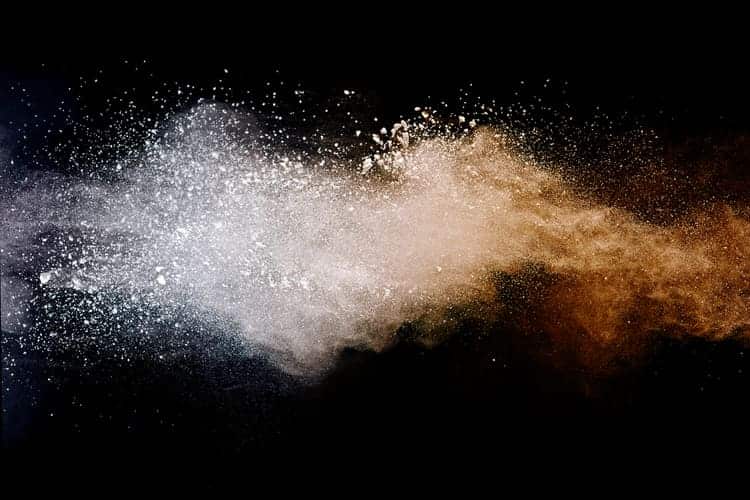
Ever since early humans learned to press their hands against cave walls and used pigments to leave their outlines, wall painting quickly turned to face painting. Researchers argue that makeup was part of a huge ritual that influenced our cultural evolution. Human curiosity spearheaded the creation of what would become the modern cosmetics manufacturing industry.
With the global market value of cosmetics expected to reach $806 billion by 2023, the future seems bright!
The desire for newer, safer, more vibrant and effective products led to millennia of technological advancements. Seeking products that were easier to manufacture and sustainable was equally as sought after as pioneering the next big shade to wow the public.
Some of the earliest commercially adopted products where powders and foundations. These highly popular products contained mixtures of many ingredients, like organic compounds, minerals, oils and pigments.
Cosmetics manufacturing is deeper than you think
On the surface, you may not realize the complexity involved in cosmetics manufacturing is more than just skin-deep. It’s estimated that a standard cosmetic product can contain up to 50 ingredients, all of which are heavy controlled.
With facial powders, the aim is to produce a desirable surface finish on the skin, meaning the particle size distribution needs to be tightly regulated. Such products are designed to reflect light in flattering angles on the face, diffuse light for an even finish on the skin, or even act as a sunscreen when materials with light-scattering properties are included.
Two common ingredients are mica and iron oxide. Mica powders are crushed from minerals and purified, with some mica powders noted for their ability to add lusher and sparkle. Interestingly, other mica powders can even have the opposite effect by adding a matte finish. Iron oxide is primarily used for introducing pigment into cosmetics. It can add undertones of color to anything from lipsticks to blushers. So if you want your makeup to sparkle, or stand out from the pack with eye-catching vibrancy, you need to measure and control particle size distribution.
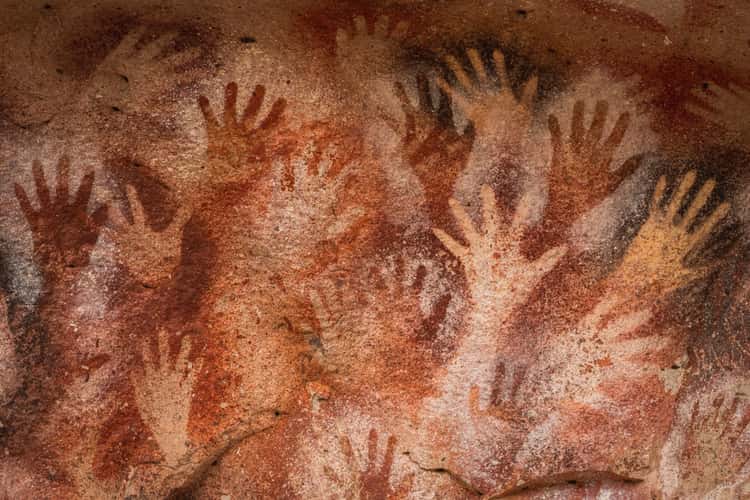
Pushing higher cosmetics safety standards
A recent study outlined elements for a tiered safety assessment approach for cosmetic powder formulations to allow increased transparency for regulators and reliability of results for consumers. This study opens a discussion regarding assessing the safety of exposure to loose particles within our respiratory system. The study states:
If a cosmetic powder has the potential to generate a dust cloud or atmosphere, then there is the potential for inhalation exposure during handling or application. Knowledge of particle size and their allocation to the three defined fractions [nasopharyngeal, tracheobronchial, pulmonary regions] becomes the next important factor for an exposure assessment.
The study concludes that larger particles greater than 30 μm would be toxicologically preferred as this would minimize inhalation exposure and lead to increased clearance from the respiratory tract and reduced exposure. Particles greater than 30 μm are captured in the nasal areas and expelled through sneezing or nose blowing. Inversely, the author noted that fine particles smaller than 10 μm have the potential to enter deeply into the lungs, raising questions about their impact on the body and the need to assess the safety of exposure. No doubt further data will emerge over time which will aid safety regulators in taking a more definitive position on particle size requirements. Nevertheless, the research underscores the need for manufactures to demonstrate control and understanding of their process.
Eyecon2 is a direct imaging particle analyser that generates real-time particle size and shape information ranging 50 -5500 μm in a variety of key processes used in cosmetics manufacturing. It delivers better process understanding and process control to increase productivity, yield, and achieve quality targets. A unique feature of Eyecon2 is its non-product contact analysis and profiling of wet or dry powders and bulk solids. This means it’s right at home in cosmetics manufacturing to ensure product quality and safety. Chat to us about how Eyecon2 can benefit you.
At InnoGlobal Technology (formerly Innopharma Technology) we’re motivated to push boundaries within industry and share our knowledge. Follow us on LinkedIn and Twitter for more exciting developments from R&D to Industry 4.0!