An end-to-end review of Laser Diffraction
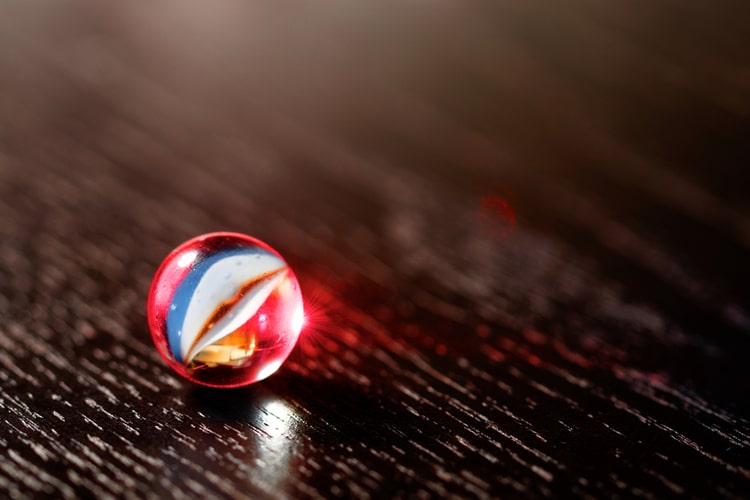
Exploring the particle size measurement landscape is challenging and time-consuming. There are several methods of particle sizing used by different industries. With over a decade of expertise in particle sizing technology, we know the difficulty the users face to determine the best method for their process. To assist you, we have created a detailed review of industry-standard methods such as laser diffraction and cutting-edge direct imaging particle size analysers, to give you an appreciation of factors to consider in your particle size distribution (PSD).
Defining laser diffraction
Laser diffraction is a method of calculating the PSD of sample material by analysing the scatter pattern of light from a sample. As the light interacts with particles, it scatters in a pattern that is detected and measured by an array of sensors. The angle and intensity of the scatter pattern correlate with the size of the particle size and makes it possible to infer particle size information from the scattered light mathematically. The particle size information for a given sample is presented as a volume fraction distribution based on the diameter of the sphere of the equivalent volume of the observed particle.
How they work
The fundamental principle governing the determination of particle size by laser diffraction is the interaction of light with a particle. When light meets a particle, the incident light is altered in a way that is usually characteristic of that particle type. Some of the interactions which can take place include reflection, refraction, absorption, and diffraction, as seen in the figure below.
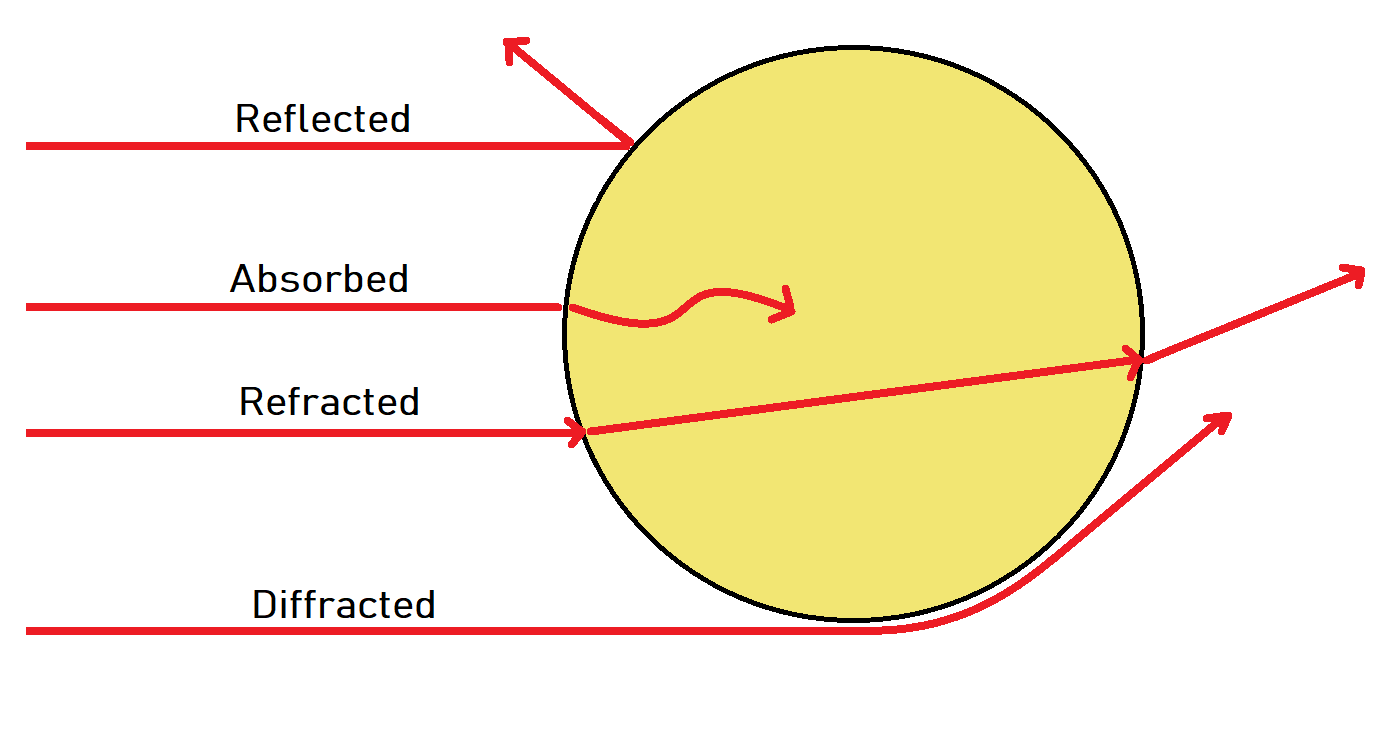
As light interacts with the particle surface, it undergoes diffraction, resulting in a distribution of scattered light, which is measured by an array of detectors and predictive models to infer particle size. The two main factors that influence scattering are light wavelength and particle size; smaller particles result in a broader scattered light distribution, for example.
Our in-house advanced particle size analyser Eyecon2, which is a direct imaging device, calculates particle size distributions based on the measurement of individual particles within a sample image. The images captured are processed by the software EyePASS™ where the particle detection algorithm identifies and measures individual particles within the captured image.
Using predictive models for measurement
Laser diffraction uses three predictive models to describe the relationship between particle size and light scattering – Fraunhofer approximation model, Rayleigh scattering model, and Mie scattering model. These models vary in their approach, and so each has suitable particle sizes over which they can accurately predict. The choice of which model to use is therefore influenced by the particle size range of interest, but also the degree of complexity of each model.
Rayleigh and Mie scattering theories are independent theories that describe two different situations. Rayleigh scattering occurs when the particle is smaller in size than the wavelength of the incident light. In comparison, Mie scattering occurs when the particle is much larger than the wavelength of the incident light. The Fraunhofer approximation is a related and simplified approximation to Mie theory and as such is applicable only to particles in and above the micrometre (µm) range, opposed to the nanometre (nm) range for the two former theories.
For example, Eyecon2 measures a multitude of particle parameters and values that are trended in real-time with live histogram and S-curve results. This allows Eyecon2 to quickly get to work once installed without requiring complex modeling
Correlation with particle properties
We learned earlier that the angle and intensity of scattered light are directly related to the size of the particle. Larger particles scatter light at lower angles and with greater intensity than smaller ones. Depending on the particle, differing angular distributions can occur, which effectively dictates the predictive model that should be used.
However, both the Rayleigh and Mie equations contain several other dependencies such as refractive index and empirical constants. This leads to the requirement of a significant amount of prior knowledge of the measurement environment. While the refractive index is readily measurable, the empirical constants are not so. Typically, manufacturers will calibrate the instrument with known particles, solving the equations in advance and creating solution matrices relating scattered light intensity to the most probable particle size.
Eyecon2 identifies particles and EyePASS™ software fits them with an ellipse that is constructed based on the crossover of light which is used by the algorithm to determine edge detection. This approach results in a tighter, smaller volume fit than the cubed diameter of an equivalent circle that fit the same particle. This allows Eyecon2 to more accurately calculate particle volume which will affect the subsequently calculated D-Values.
Limitations
As with any scientific method, there a few restrictions, caveats, and difficulties surrounding the use of laser diffraction and direct imagining particle size analysers for PSD. We have detailed some limitation for each measurement system below:
Laser diffraction:
- The optical properties of the sample and the surrounding medium must be known before the optical model can be established.
- The refractive index of a particle may not permit the use of laser diffraction
Direct image analysis:
- The focal length of the system may be limited, meaning samples must be adequately close to being measurable.
- The measurement system may also be sensitive to transparent materials such as glass and may lead to reduced accuracy in measurement.
For more information, view our detailed application note where we deep dive further into laser diffraction and many more industry-standard PSD measurement methods.
We at InnoGlobal Technology (formerly Innopharma Technology) are motivated to push boundaries in the pharmaceutical industry and share our knowledge. Follow us on LinkedIn and Twitter for more exciting developments from R&D to Industry 4.0!